Jim Campbell passes Chapin's leadership role to WNY native Tim Onello
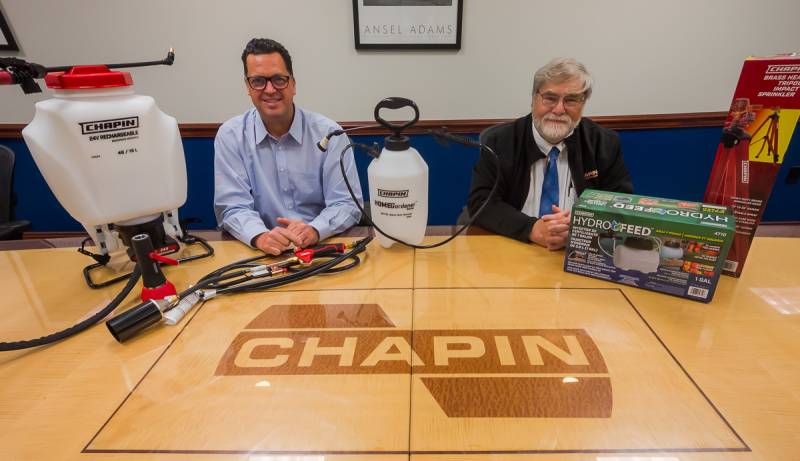
Photo by Howard Owens.
As Chapin International prepares to celebrate its 140th year in business, it will do so with a new president and CEO in place, a Western New York native whose manufacturing career has taken him across the United States.
Chapin was founded in Oakfield and remains based in Batavia, with its headquarters on Ellicott Street. The company's growth has led to the opening or acquisition of plants in other states and parts of the world.
With all of that, and the challenging business climate in New York, Chapin remains committed to Batavia, said the new CEO, Tim Onello.
"I think that is where our priority is," Onello told The Batavian in an exclusive joint interview On Thursday with Jim Campbell, who is retiring as president and CEO. "I know the company is 100 percent committed to this area and to ensuring we're a good employer in the region. So, yes, our number one commitment is to stay here in Batavia."
Onello said he is looking forward to continuing the growth Chapin has enjoyed under Campbell's leadership. Campbell was Dave Ward's successor. After Ward, Campbell was the second non-family member to run Chapin. With 20 years in the CEO seat, Campell was the longest-serving person in that position.
Though Onello has been an executive with lawn and garden manufacturing companies throughout much of his business career, Chapin's line of sprayers and related products is a slightly new field to him.
"I think what attracted me to the company was, first, all of the product range," Onello said. "Even though it's a little bit outside of my background, my background is hand tools and power tools, a lot of them are sold in the same channels as Chapin."
That mix of products at Chapin and its track record of growth is an opportunity and challenge, Onello suggested.
"Where's that next growth coming from? So, I think part of where we'll dig in with the team is just to find out how can we grow the business and take it to the next level," Onello said. "Jim and team have done such a great job at growing this business over the past 20 years, and I think Jim took it four times where it used to be. It's my job, with all the marketing and product experience, to really look at adjacent areas for this company to manufacture new products and take it to that next level."
Onello was VP and general manager of ITW, a Fortune 200 company. While employed by ITW, he was based in San Luis Obispo, Calif. Prior to joining ITW, he spent nearly 12 years with JPW Industries in Nashville, rising to the position of VP and general manager.
He has MBAs from Thunderbird School of Global Management and the University of Nevada-Las Vegas and a bachelor of science in marketing and psychology from Northern Michigan University.
Chapin was founded in 1884 in the back of a hardware store in Oakfield, where R.E. Chapin made oil storage containers for oil lamps. In the early 1900s, the company moved to Batavia and started manufacturing garden sprayers.
Today, the company has six major product lines with more than 650 different items for sale to retail and business customers.
Campbell is proud of the company's accomplishments during his tenure.
"If you're not growing, you shrink," he said, which is why the company works through five-year strategic growth plans. The most recent plan expires as he exits.
"This will be the first year that we didn't quite meet the strat plan," Campbell said. "That's because in the strat plan was another acquisition for about $40 million. We didn't do another acquisition. That's the only part of the five-year plan we didn't meet. All the organic growth we did meet, and (the company) is still growing. We should be able to make another $50 million to $60 million in three or four years."
That's gross revenue.
Chapin isn't a publicly traded company, so it generally does not disclose revenue and profits, but publicly traded companies, such as another big manufacturer in Batavia, Graham Corp., are required to release financial reports, and so Campbell offered this comparison: "We do more dollars than Graham."
Graham's reported revenue for 2023 was $147.1 million.
Campbell's role in helping the board of directors select a new CEO focused primarily on ensuring the board understood the complexities of the job. He put together a job description that filled a three-ring binder with 150 pages.
He said job candidates also agreed to a psychological profile, which is common in the business world these days, especially for executive positions.
Onello was attracted to the job not only because of the product line but also because it offered him a chance to move back home to raise his three teenage daughters close to family in Western New York.
"I grew up in Cheektowaga and went to schools in West Seneca," Onello said. "I have a ton of family in Buffalo and was bringing my family back here three times a year to visit the area, so when the opportunity came up to return to Western New York, to be able to jump into an adjacent industry, to be back with family and friends, it was just ideal."
Onello said he was impressed with Chapin's culture and praised Campbell's ability to maintain a loyal workforce.
"One of the biggest things, it's always about the people, right?" Onello said. "I think Jim's built an incredible culture here where you have long, tenured, loyal workers who really care about the brand and care about the company. There's a lot of pride in the company. Many employees have 30 years or 40 years of tenure, and that just doesn't happen in so many other areas. That loyalty to the brand, to the company, is really exciting."
Campbell's plans in retirement — he's rooted in Western New York with a residence just inside of Erie County from Pembroke — and a plot of land in Pembroke with an orchard and elderberries and a big barn, don’t include moving elsewhere.
He said he plans to spend more time with his wife Caite. They also have a cottage in Canada.
"We're a real outdoor, hunting and fishing kind of family," Campbell said.
He also enjoys blacksmithing, primarily making knives.
As for Onello, he doesn't have time for many hobbies. His daughters are 13 and 15.
"When I'm not working, I'm usually chasing them around, taking them to their events and sports," Onello said. "Of course, naturally, I look forward to being able to go to a few Bills and Sabres games now that I'm back in the region."