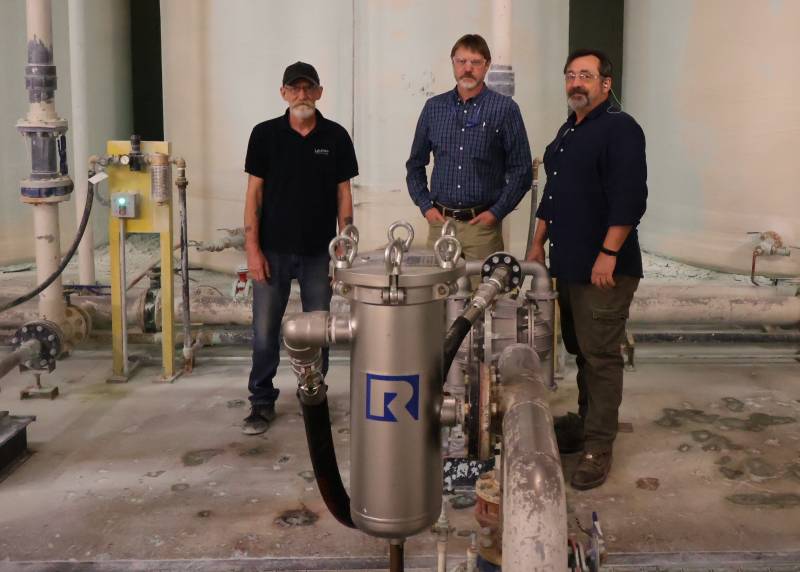
Press Release:
Lapp Insulators Co. LLC changed a decades-old process to incorporate new technology and equipment that results in energy savings, lower operating costs, and a safer work environment. The changes also earned the Le Roy-based company $27,000 in energy efficiency incentives from National Grid.
Lapp is a leading manufacturer of high-voltage insulators for electricity substations. The company recently replaced a 150-horsepower, high-pressure air compressor that had been used for 40 years with three Wilden Air diaphragm pumps to push 1.5 tons of liquid clay through its production lines. Lapp officials are pleased with the results, which include a 70 percent energy savings.
“This was a major change to our process,” said Facilities Manager Ron Richards, who worked with National Grid Energy Efficiency Specialist Jay Snyder to identify the opportunity and execute a plan to install the new pumps.
“By collaborating with Jay and sharing ideas, we significantly improved our process, which means less downtime and more productivity. The new pumps make our employees and work environment safer, and we anticipate long-term operations cost and maintenance savings. We’re making higher quality products and are doing more with less.”
Richards said that the previous production process required approximately three times as much energy. The aqua-colored, soft, squishy clay is the main ingredient that Lapp uses to shape, fire, and glaze ceramic insulators that are used at electricity substations across North America. Around 130 people work at the Le Roy facility, which dates to 1916.
“At the foundation of our energy efficiency program is the ability to collaborate and learn from our customers so that we can better understand their needs and work together to find ways to lower their costs and reduce energy use,” said National Grid Regional Director Ken Kujawa. “When costs can be lowered and kept low for companies like Lapp Insulators, it can help them to grow, keep their facilities local, and build their workforces.”
“Our ability to work with Lapp Insulators to achieve energy efficiency goals and streamline production illustrates National Grid’s commitment to them, as well as all local manufacturers,” added Snyder. “The solution that we developed with Lapp has resulted in additional discussions about future projects to improve efficiencies and reduce costs in other areas of the facility, including lighting, an air compressor, dust collector motors, and an air dryer.”
Funding for the Lapp project was provided through National Grid’s Energy Efficiency Program, which includes financial incentives for commercial and industrial customers who reduce electricity costs. Incentives are available for customers who install energy-efficient lighting, controls, HVAC equipment, motors/electronic speed controls, and other systems that reduce energy use and/or enhance productivity.